When it comes to construction projects, one of the foundational elements—quite literally—is the concrete slab. Whether you’re building a home, a commercial space, or laying the groundwork for a significant development, understanding the cost of a concrete slab is essential for budgeting and planning.
Hiring qualified concrete contractors is crucial for ensuring the success of your concrete slab projects. These professionals can guide you through the process of pouring concrete slabs, obtaining necessary permits, and applying proper waterproofing techniques to prevent moisture issues. In this blog post, we’ll unravel the factors affecting concrete slab costs and provide insights tailored for concrete companies, contractors, and property developers.
What is a Concrete Slab?
A concrete slab is a flat, horizontal surface made from poured concrete, commonly used to pave outdoor areas or support the weight of structures. This versatile and durable construction element is a popular choice for various applications, including patios, driveways, foundations, and garage floors. Its affordability and strength make it an essential component in many construction projects, providing a reliable base that can withstand significant wear and tear.
Types of Concrete Slabs
Concrete slabs come in several types, each suited to different applications and offering unique benefits:
- Plain Concrete Slabs: The most common type, plain concrete slabs are used for various applications, including patios, driveways, and garage floors. They provide a solid, durable surface that can handle everyday use.
- Reinforced Concrete Slabs: These slabs incorporate wire mesh or rebar to enhance their strength and durability, making them ideal for heavy-duty applications with additional support.
- Stamped Concrete Slabs: Designed to mimic the appearance of natural stone or other materials, stamped concrete slabs offer a decorative finish that adds aesthetic appeal to outdoor spaces.
- Stained Concrete Slabs: By applying stains, these slabs achieve a unique, decorative look, perfect for enhancing the visual appeal of patios and other outdoor areas.
- Colored Concrete Slabs: Pigments are added to the concrete mix to create slabs in specific colors or designs, allowing for customized and visually striking surfaces.
.jpg?width=600&height=400&name=patio-living-space-with-comfortable-seating-around-2023-11-27-05-06-21-utc%20(2).jpg)
Common Applications
Concrete slabs are incredibly versatile and are used in a variety of applications:
- Patios: Due to their durability and versatility, concrete slabs are a popular choice for creating outdoor patios and decks that can withstand the elements and heavy foot traffic.
- Driveways: Concrete slabs are ideal for driveways, offering the strength needed to support vehicles and resist wear from frequent use.
- Foundations: Many homes and buildings rely on concrete slabs as their foundation, providing a stable and durable base that supports the entire structure.
- Garage Floors: Concrete slabs are commonly used for garage floors, offering a durable and easy-to-maintain surface that can handle the weight of vehicles and resist stains and damage.
The Importance of Accurate Cost Estimation in Concrete Projects
Accurate cost estimation is crucial in the construction industry to avoid project delays and financial setbacks. For property developers, concrete slabs form the basis of many structures, making cost calculations fundamental.
In any concrete project, understanding the challenges and costs associated with pouring concrete, such as creating a concrete slab foundation, is essential to ensure accurate budgeting and resource allocation.
Here are a few consequences that can happen when cost estimations are incorrect:
- Running out of budget mid-project causes delays and work stoppage, leading to additional costs.
- Overbudgeting can also lead to wasted resources, which could have been allocated elsewhere in the project.
- The inaccurate estimation may result in underbidding or overcharging clients, leading to loss of profits and reputation damage.
Factors Influencing Concrete Slab Costs per Square Foot
Material Costs
Material costs significantly impact the overall expense of a concrete slab. Concrete prices vary depending on the type and quality of materials used, such as cement, sand, and aggregates. Fluctuations in material prices can affect the final cost, making it essential for concrete companies and contractors to stay updated with current market rates.
The choice of concrete mix and slab thickness also plays a role in determining costs. Different mixes are suitable for various applications, each with unique characteristics and price points. Thicker slabs can accommodate greater weight and are essential for specific applications, influencing the volume of concrete required and overall costs. Understanding the specific requirements of a project, including the appropriate slab thickness, can help identify the most cost-effective mix without compromising quality.
Labor Expenses
Labor is another crucial component in the cost of a concrete slab. The complexity of the project and the skill level required can influence labor expenses. Hiring experienced professionals ensures quality and efficiency but may come at a higher price. It's essential for contractors to balance labor costs while maintaining high standards of workmanship.
In addition to skilled labor, the time required to complete the project affects costs. Faster completion times might demand additional workforce or specialized equipment, adding to the overall expenditure. Proper scheduling and resource allocation can help manage labor costs effectively.
Site Preparation and Accessibility
Site preparation is a critical step in laying a concrete slab and can significantly impact the cost. Factors such as soil condition, grading, and drainage need careful consideration. Poor site conditions may require additional work, such as excavation or reinforcement, increasing costs.
Accessibility to the site is another consideration. Difficult-to-reach locations may require specialized equipment or extended labor hours, affecting the project's budget. Proper planning and assessment of site conditions can help mitigate unexpected expenses.
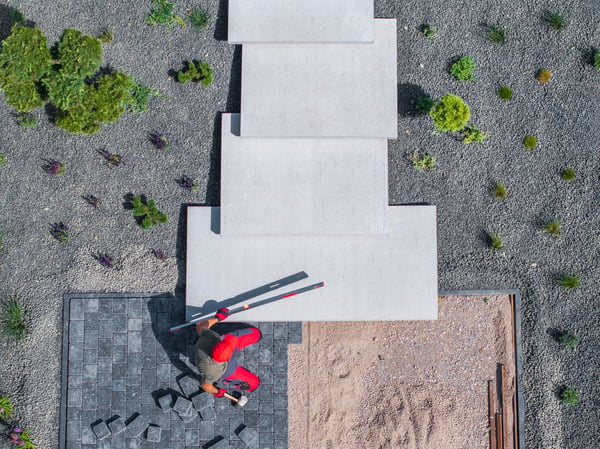
Regional Concrete Slab Costs
National Average Costs
The cost of a concrete slab can vary widely depending on several factors, including the slab’s size, thickness, and location.
On average, the national cost for a concrete slab is around $6.60 per square foot, with prices typically ranging from $4.34 to $7.73 per square foot. However, regional differences can significantly impact these costs due to variations in labor costs, material prices, and local regulations.
Estimating Concrete Slab Costs
Calculating Materials Needed
Accurate estimation of materials is vital for cost calculation. Begin by determining the slab’s dimensions, including thickness, length, and width. Most concrete slabs are typically 4 to 6 inches thick and can last 30 to 40 years, or even up to 100 years with proper maintenance. This information helps calculate the volume of concrete required, ensuring enough material is ordered, avoiding wastage or shortages.
Property developers and contractors should collaborate with suppliers to get the best deals on materials. Bulk purchasing or long-term contracts can offer cost-saving opportunities, contributing to more competitive project bids and better profit margins.
Considering Additional Features
Additional features such as rebar, insulation, or decorative finishes can elevate the functionality and aesthetic of a concrete slab but come at a cost. When considering concrete slab installation, it’s essential to assess these features’ necessity based on the project’s scope and budget constraints.
Communication with clients about optional features and their benefits can influence the project’s direction. Providing detailed explanations and cost breakdowns helps clients make informed decisions that align with their vision and financial capacity.
Leveraging Technology in Cost Estimation
Modern technology offers tools and software to enhance the accuracy of cost estimations. Advanced software solutions can automate calculations, consider regional cost variations, and generate detailed reports, saving time and reducing human error.
Concrete companies and contractors can leverage technology to improve efficiency and accuracy. Investing in training for staff to utilize these tools effectively can provide a competitive edge and reassure clients of precise cost management.
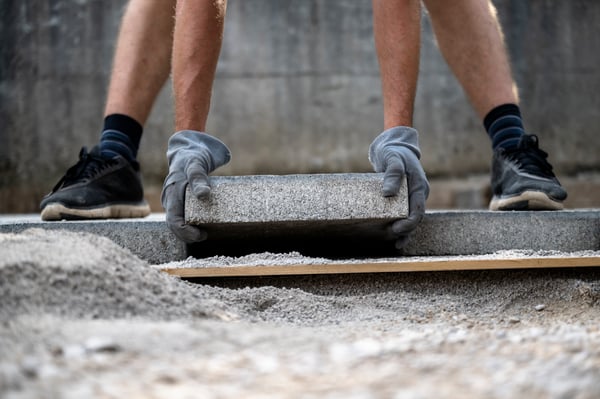
Common Misconceptions in Concrete Slab Costing
Overlooking Hidden Costs
A common mistake is underestimating hidden costs associated with concrete slabs. Costs like permits, inspections, and potential delays are often overlooked. Comprehensive project planning should include these expenses to present clients with a realistic budget.
Educating clients about potential hidden costs fosters transparency and trust. Clear communication ensures all parties are aligned, creating a smoother project execution process and reducing disputes over unexpected charges.
Assuming Uniform Pricing
Another misconception is that concrete slabs have uniform pricing across different projects. Various factors, such as location, project scale, and design requirements, lead to significant price variations. Each project should be evaluated individually to provide accurate cost estimates.
By tailoring cost estimations to specific project parameters, contractors and developers can offer more precise proposals. This approach not only improves client satisfaction but also minimizes the risk of financial loss due to inaccurate budgeting.
Ignoring Long-term Value
Focusing solely on initial costs can sometimes lead to overlooking long-term value. A cheaper concrete mix or lower-quality labor might save money upfront but could result in higher maintenance costs or structural issues later. Evaluating the long-term benefits and costs is crucial for decision-making.
Highlighting the advantages of investing in quality materials and skilled labor can persuade clients to opt for solutions that ensure durability and reduce future expenses. Positioning as a provider of value-driven solutions enhances brand reputation and client loyalty.
Conclusion
Understanding the cost of a concrete slab involves more than just the price of materials and labor. It's about comprehensive planning, accurate estimation, and strategic decision-making. For concrete companies, contractors, and property developers, mastering these aspects leads to successful projects and satisfied clients.
With the insights and tips provided in this post, you're equipped to tackle concrete slab costing with confidence. By staying informed and adaptable, you pave the way for efficient project management and robust business growth.
Looking for a trusted partner for all your concrete grinding needs? Look no further than Onfloor. At Onfloor we specialize in robust concrete grinders that are also lightweight and versatile. Best of all? All of our concrete grinders come equipped with our quick change tooling technology so you can tackle multiple applications with one machine!
8 comments