If you're put to the task of resurfacing a concrete floor, you don't want to be left doing it by hand with a floor scraper. You also probably don't want to have to deal with a bunch of dangerous messy chemicals.
Floor preparation for big floor jobs is often times the bulk of the work. That's why we are here to talk about how to add ease and speed up your floor jobs with a concrete grinder.
Concrete grinders come in many different sizes and are used in various applications. If you're interested in learning more about them, read on to find out.
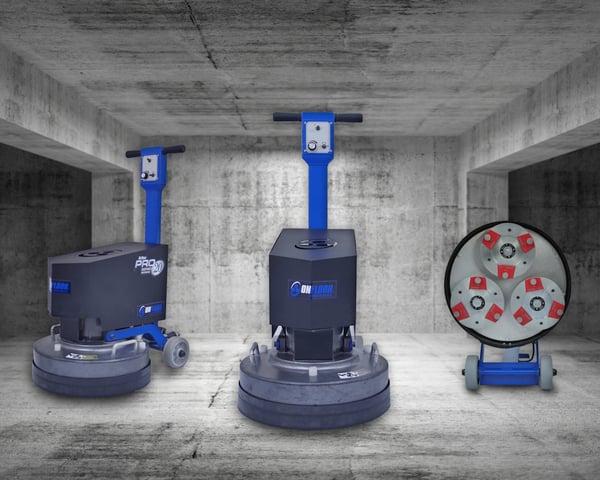
What Applications Are They Used For?
Concrete restoration can oftentimes require tedious and laborious floor preparation. Pre-existing coatings, surface imperfections, residue, organic matter, oxidation, and other contaminants are some of the things that build up on floors and need removal in order to restore.
- paint removal, epoxies, clear coats
- tile residue, glue, adhesives
- leveling uneven surfaces
- stains, oil, grease, dirt
- old sealers or coatings
- polishing concrete surface
Concrete grinders come in handy wherever a pre-existing concrete floor needs to be completely smooth and free of any organic or non-organic material—typically for concrete restoration sealing purposes.
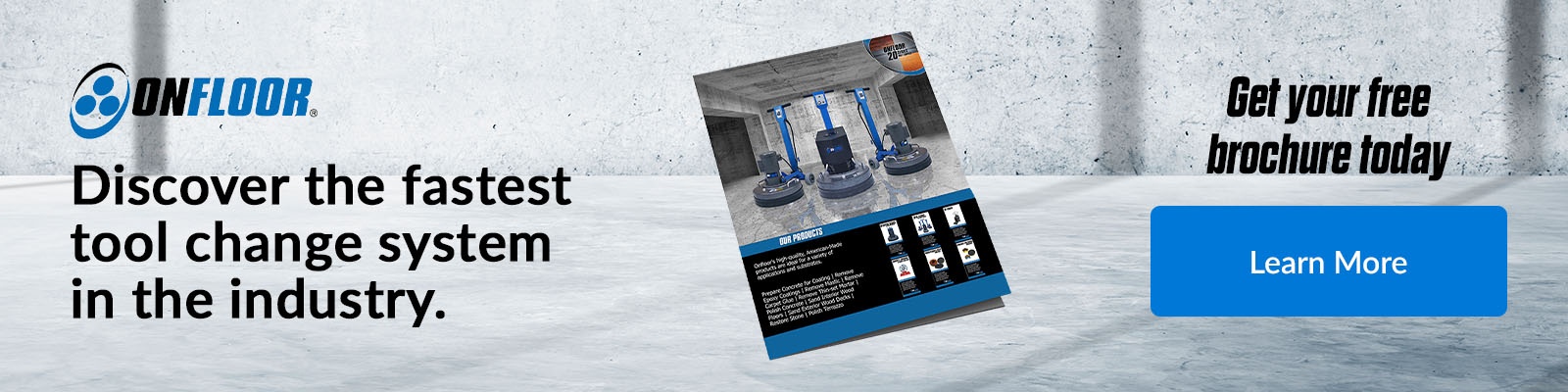
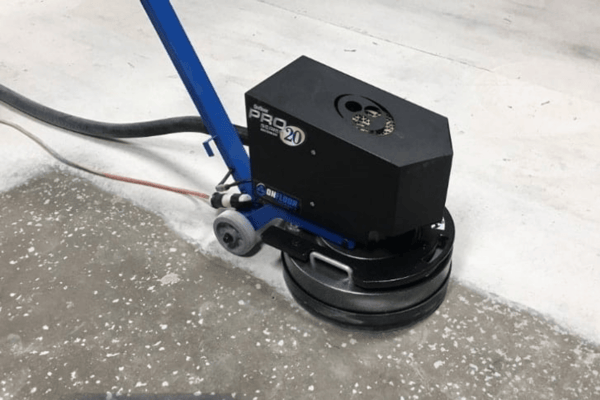
How Does a Concrete Grinder Work?
A concrete grinder is a machine used as a finishing tool for floor restoration. It levels and smooths out surfaces by the use of rotating discs engineered with abrasive diamond bits.
Concrete grinders can be handheld, walk-behind, or even ridden. They are powered by gas, propane gas, and electricity.
Gas-powered grinders typically guarantee a more consistent power source compared to the others. They generally should only be used for outdoor applications.
Hand-Held Concrete Grinders
At times walk-behind grinders aren't able to get into corners or tight areas. That's where hand-held grinders come in handy. They're smaller and offer more maneuverability in smaller areas like corners, etc.
Walk-Behind Concrete Grinders
When large areas of concrete need resurfacing, walk-behind grinders are used. There are many different types and sizes of walk-behind grinders available. The two main categories are rotary grinders and planetary grinders.
Rotary Grinders
Rotary grinders use a single large pad that spins at high speeds. Because these grinders have a higher rotational speed and are heavier, they are great for jobs that require heavy removal of surface matter.
A skilled operator will use the advantage of a heavy machine with higher-rotation speed to remove thick layers of mastic or paint. Rotary grinders can also create a better polish on concrete floors if done right.
However, because they're heavier and have high-speed rotating discs, they're often more difficult to maneuver. These grinders take more training in order to operate skillfully. Rotary grinders can often leave irregular scratch patterns in the concrete if the operator is not correctly trained.
Planetary Grinders
Instead of only using one disc like the rotary grinder, planetary grinders make use of multiple pads to get the job done. These pads spin simultaneously albeit at different speeds. Multiple discs with different abrasiveness allow a planetary grinder to remove material and finish a concrete floor at the same time.
These grinders are more lightweight and easier to maneuver than the rotary grinder. Their design allows the operator to maneuver in straight lines without having to struggle.
Because they're more lightweight and easier to operate, planetary grinders work great for smaller jobs. They're ideal for jobs that don't require heavy concrete restoration—like smoothing and finishing a residential garage floor for an epoxy coating.
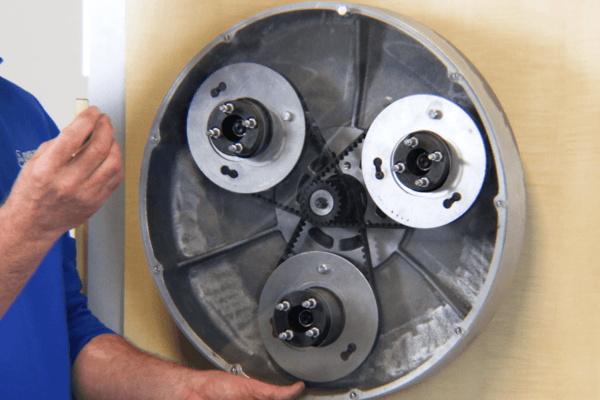
What Is HeadCount?
Headcount is the amount of grinding discs a grinder is fitted with. The number of discs a grinder has will determine what kind of job it is used for as well as how much area it can cover with one pass.
Grinders can have one to four heads. Generally speaking, grinders with more heads cover larger areas. They also exert less pressure and are best for finishing projects.
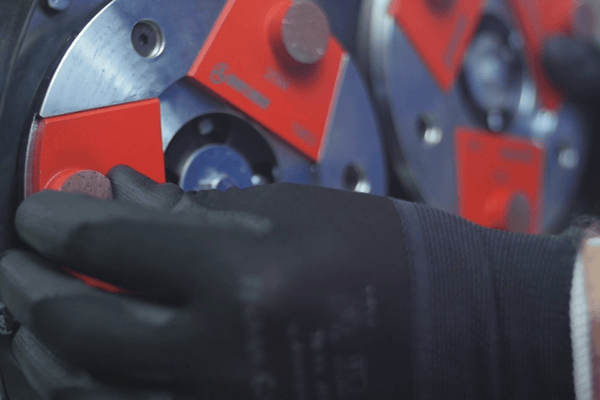
Grinder Attachments and Diamond Tools
There are a few different grinding attachments used with grinders and they all serve their purpose. The three most common types of attachments are silicon-carbide-impregnated grinding stones, tungsten-carbide inserts, and diamond-segmented tooling.
Silicon-Carbide Grinding Stone
A silicon-carbide attachment stone is an excellent choice for smoothing out trowel marks or rough finishes or leaving out high spots. These stones are available in fine grits as well as course grits. Because these stones are susceptible to clogging, they're not preferred for jobs that require removing any type of paint or coating on a concrete floor.
Tungsten-Carbide Inserts
Tungsten-carbide inserts use a carbide-tipped block that has beveled edges. These inserts are capable of stripping heavy material or coating on concrete floors without digging into it.
They work best at removing material that is thicker than 1/16". Some of their applications include removing thick layers of paint, resins, tar, adhesives, rubber deposits, and industrial chemical build up.
Diamond Tooling
Diamond tooling plates consist of diamond segments that are bonded to a backing plate or sometimes a removable block insert. The diamonds are embedded into a metal or resin block that eventually wears away from use—exposing more diamond segmented layers.
Diamond tools work best for jobs that require removing thin films of coatings that have a high hardness value, such as urethanes and epoxies. They come in various grits and their applications include removing minor surface imperfections and polishing.
One thing that is often overlooked when using diamond tooling is the bond hardness of the material that holds the diamond segments. In order to achieve the best efficiency and to give maximum life to the tool, use a hard bond when grinding soft materials and a soft bond for hard materials.
Grinding Dry vs Wet
When using a grinder for floor restoration, there sometimes is a question of whether to dry or wet grind. Most floor grinder operators will grind dry for the primary reason of not having to clean up a soupy mess.
Not only that, but grinding dry allows operators to see the floor better while grinding wet can hide low spots. Grinding wet can be used in situations where dust is a big concern.
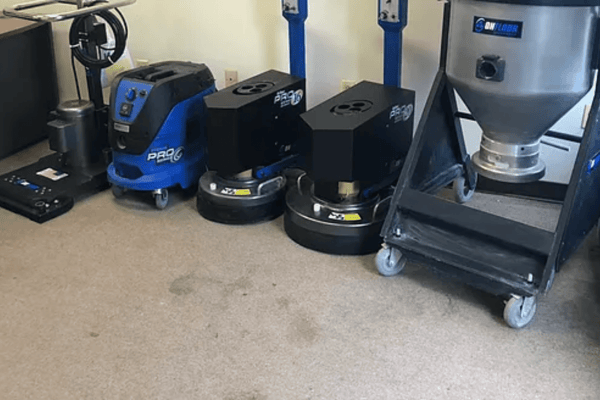
Choose the Right Grinder for the Job
Some concrete grinders are more versatile than others while some grinders are more job-specific and take more skill to operate. There's no doubt that using the right type of high-quality grinder can speed up job productivity and deliver professional results.
If you're wondering how to choose the right concrete grinder for your job, check out our article for more useful tips.
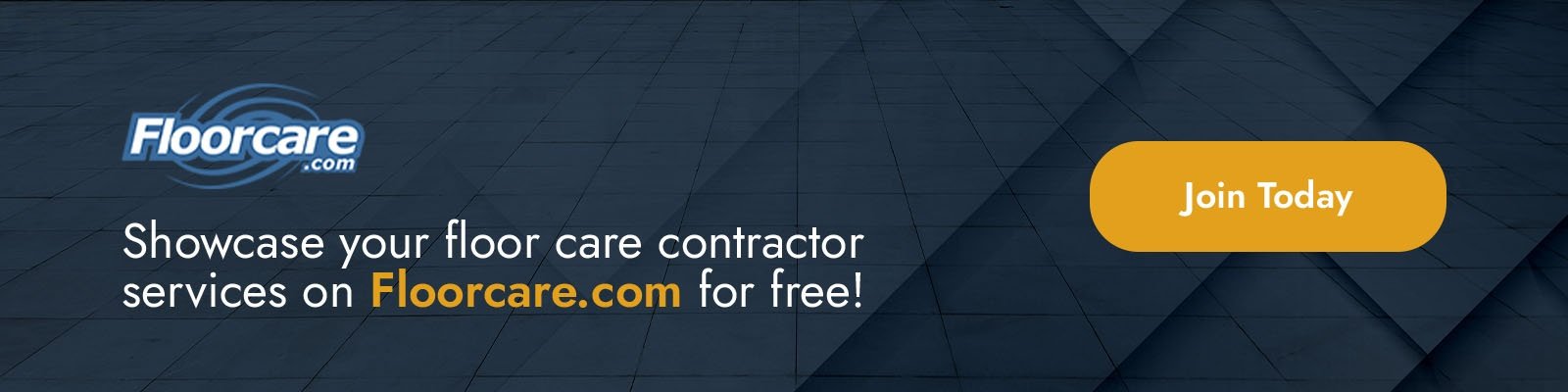
3 comments