Forklifts, heavy loads, and other vehicular machinery can inflict massive strain on the flooring in industrial and commercial facilities. Not only does the finish deteriorate, but the concrete itself can get damaged over time. That is why flooring companies need to stop this process sooner because replacing a worn-out concrete slab can lead to higher cost, vast downturn, and lost production.
5 Insightful Benefits of Concrete Resurfacing
Concrete floor resurfacing can be an efficient solution that gives any industrial floor a much-needed facelift. While numerous factors contribute to the successful restoration of concrete, including surface prep, resurfacing gives flooring companies some clear and unique advantages.
- Resurfaced concrete can be open to heavy-load traffic in one or two days.
- Resurfacers eliminate the pain points (labor, time, and other expenses) of removing the existing concrete and pour a new slab.
- No specialized training or skills are needed to apply a resurfacer.
- Concrete restored with commercial equipment can be stamped, stained, or colored for an extra touch of aesthetics.
- Beyond restoration, resurfacers shield concrete floors, making it possible for a variety of repairs.
However, flooring companies need more than just a high level of resurfacing expertise to make things tick. They need an arsenal of high-level equipment and tools too.
Below we explore how flooring companies can use commercial equipment to resurface concrete successfully.
HOW TO RESURFACE
Surface Preparation
Ultimately, the effectiveness of surface preparation comes down to the choice of equipment. The wrong set of tools can be the difference between a well-prepared floor and a rugged surface.
Flooring companies can start by preparing the surface. It should be void of cracks larger than ¼" deep or wide, structurally robust, and repaired fully.
This process requires thoroughly disinfecting the concrete to remove coatings, dirt, grease, oil, and other contaminants. It involves:
1. Shot Blasting
Perfect for stripping a surface, shot blasting is regarded as the most time-saving or cost-effective method. It gives a coarse, open-pore texture that improves aesthetic displays.
- Shot blasters- which primarily consist of a blade-like wheel- work by propelling steel shots to fracture the surface layer. They remove concrete imperfections of every nature. By adjusting the equipment's shot flow, acceleration, rate, and size, flooring companies can achieve a full range of surface profiles, ensuring a compact, long-lasting bond.
- Key Point: Flooring companies are well aware of the impact a shot blaster's versatility can have on surface removal. However, you might have to consider other equipment for elastomeric and rubbery coatings, as they tend to deflect the steel shot.
2. Scarifying
Scarifying, also called milling or planning, strips the surface more aggressively and faster than grinding action. That's because scarifiers work by abrading and rupturing existing coatings. Multi-tipped carbon cutters rotate at top speeds to chip and pummel away at concrete surfaces. You can choose from a variety of profiles of interchangeable cutter assemblies to attain the style you need for each task.
%20(1).jpg?width=600&height=450&name=OF20Pro%20Diamabrush%20Acrylic%20(7)%20(1).jpg)
3. Grinding
Unlike shot blasters, concrete grinders have horizontally rotating discs, which give concrete floors a much smoother edge. Flooring companies can use them to prepare a floor right before smearing paint or a thin coating.
Grinding involves a multitude of jobs, from opening pores of the surface to light texturing. But the depth of the surface removal is limited to 1/8", depending on the type of attachment you use. Changing grinding attachments can give you a lot of versatility. Grinders can achieve a polish effect, especially when working on dense, hard concrete.
4. Cleaning
Cleaning is the ultimate step in surface preparation. Once you are done fracturing the surface, it's time to WASH away the residue. Flooring companies can use a 3,500 psi pressure washer to open up pores in the concrete and remove any worn-out sectors. This helps a great deal in creating a strong bond with the resurfacer. While preparing the surface, control joints and expansion joints must be maintained using a weather-stripping tape.
Mixing
A resurfacers workability and longevity depend on water content. Flooring companies should follow the ratios as stipulated by the manufacturer.
A regular paddle mixer and commercial-grade grill are enough to mix a 40-pound bag of resurfacer with a five-gallon container for 3-4 minutes. In this quantity, a high-end resurfacer has about 20 minutes of working time, which is plenty to cover 90-square feet as a skim coat or 20-square feet at ¼" thick.
For large-scale jobs, a mechanical mortar mixer can help mix 6-8 bags of resurfacer. But 3-5 person crew will have to pour it and wind up in 30 minutes or less.
Application
Before placing and spreading the resurfacer, flooring companies should saturate the concrete with enough water. Then remove any standing water. A two-fold process follows: pouring the resurfacer on the concrete in a single-foot wide strips and swabbing the material around the surface using a long-handled squeegee. There should be sufficient pressure to work the resurfacer into pores and build a marginal 1/8" thickness. For hard-to-reach edges and corners, a masonry brush can help to apply the material.
Key Point: Avoid OVERLOADING the resurfacer.
A few minutes after applying the resurfacer (not more than 5), pull a concrete finishing broom over and across the worked concrete. It should also be perpendicular to vehicle traffic to provide a non-skid, textured surface. Often, the first coat of resurfacer is sufficient to cover the existing concrete surface; however, if the second coat is a necessity, then the first coat can remain untroubled until it can handle light traffic. (For precise timings, flooring companies should refer to the datasheet of the resurfacer in the manufacturer's guide).
Curing
Flooring companies that take on large projects know the value of curing. Giving the restored concrete enough time to harden ensures that the surface is compact enough to handle traffic. When ready, spray the surface with a gentle mist. This should be 24-48 hours after working the resurfacer to prevent premature stressing and plastic shrinkage cracks during the curing procedure.
Key Point: The durability and appearance of any concrete surface is susceptible to varying weather conditions. Flooring companies should protect the resurfaced area at least 8 hours after pouring.
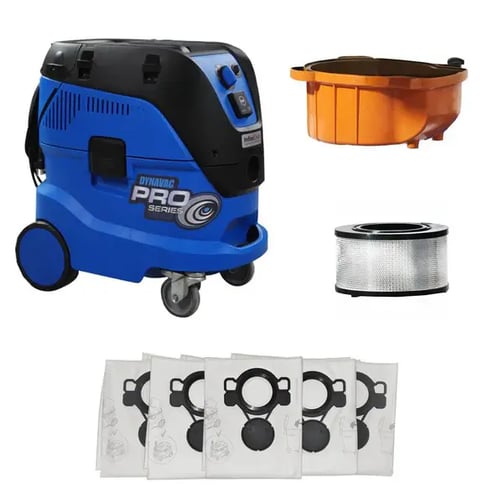
Additional Equipment for Concrete Resurfacing
These high-powered, ride-on-floor machines are ideal for floor removal- both commercial and industrial. Besides concrete, they are capable of stripping hard flooring- from hardwood and ceramic to elastomeric coating and VCT. They are perfect for sizeable jobs (small-medium surface removal) because they require little or no labor.
There is an array of scrappers to choose from at Onfloor, including high-power electric scrappers. Many are equipped with robust converters that ensure safe indoor-use and clean air.
Flooring companies can agree that resurfacing is a messy task. Using cutting-edge dust collectors improves air quality and safety and eliminates dust. This allows professionals to follow the scratch pattern as they grind.
All heavy-duty equipment requires a potent source of energy. This is precisely the case when flooring companies want to resurface concrete or even prepare it. Make sure you outsource powerful generators whenever you are replacing worn-out concrete floors.
Other high-end resurfacing equipment at Onfloor include:
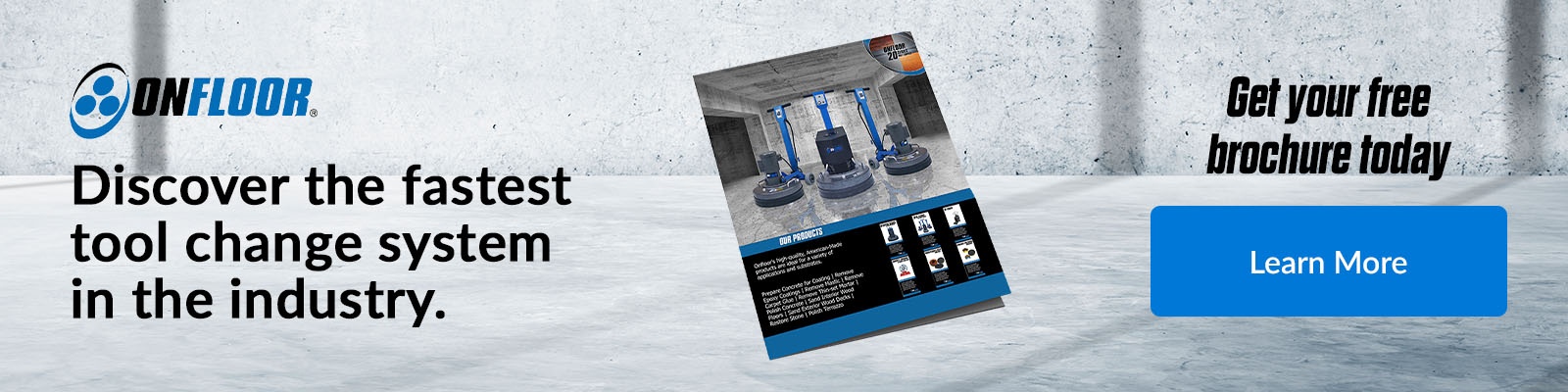
The Need for Concrete Resurfacing
Is the surface completely worn out, or does it need a simple repair? Many repair options can eliminate disposal problems, conserve resources, and save you cash. But concrete resurfacing using premium commercial equipment can help flooring companies in:
- Updating old finishes
- Fixing cracks
- Covering unsightly concrete
- Addressing discoloration
- Hiding surface imperfections
Bottom Line
Flooring companies have to select the ideal resurfacing equipment depending on the severity of the concrete damage. Whatever the surface condition, Onfloor Technologies boasts full-range, high-quality, and reliable commercial equipment.
If you have any queries, don't hesitate to call any of our professionals at Onfloor Technologies, and we will be more than willing to lend a hand.
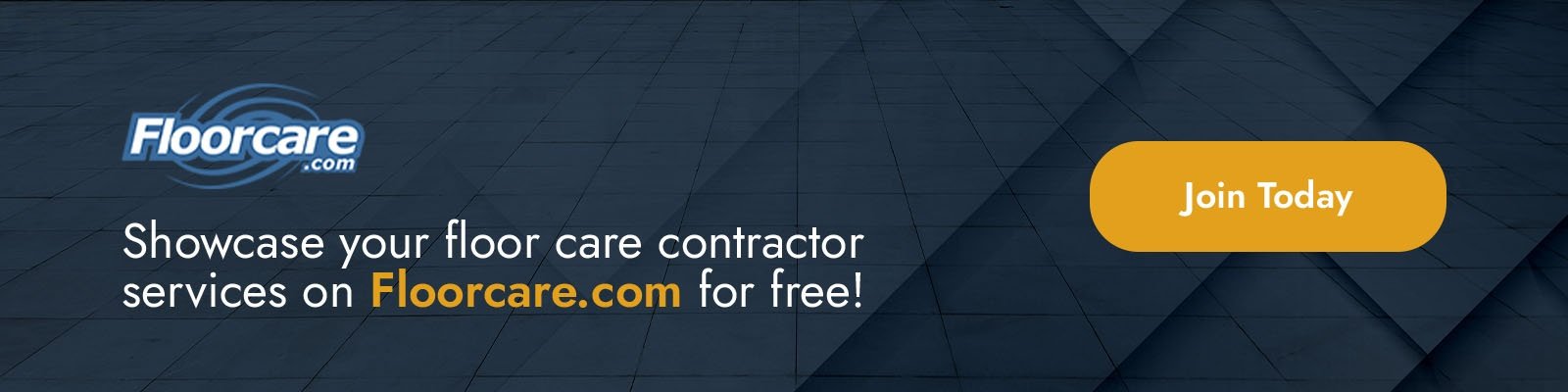
0 comments