Supply chain issues have been around for ages, from shortages on a battlefield to a construction job site, there is no escape to this issue—only that it manifests in different ways. In this article, we are going to focus on how flooring contractors can combat supply chain issues while still ensuring that the job gets done.
According to Pardis Pishdad-Bozorgi, director of the Smart Built Environment Eco-System Laboratory and associate professor in the School of Building Construction at Georgia Tech, what the industry is experiencing today is a "snowball effect.” The construction trade is facing supply chain issues related to the production of the building materials, and isn’t receiving materials in time for projects, as an adverse effect of the pandemic. This current tide forced the industry to be dynamic and innovative. Contractors are looking for alternate suppliers, and in some cases, they are importing materials from China and other parts of the world.
In this article, we will explore the different challenges surrounding supply chain disruptions and how flooring contractors can mitigate these challenges.
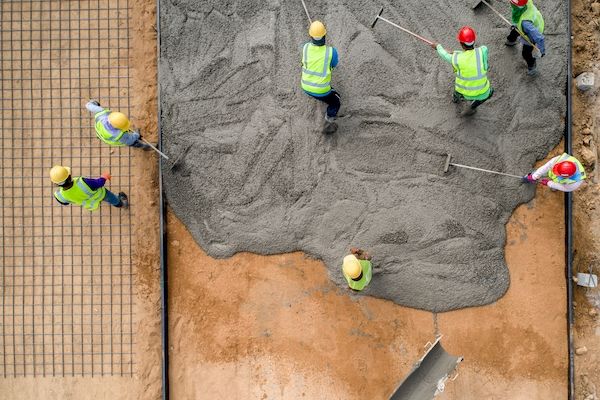
Problems Affecting the Construction Supply Chain
There is no rosy way to paint the recent years: they brought about struggles to different industries and the construction business. Contractors are responsible for addressing supply chain challenges and many hurdles have and will shape the way we respond to this crisis. Here are some of the supply chain issues faced by flooring contractors and the whole construction industry today.
1. Price Escalations, Cost of Materials and Transportation
The increasing costs of critical construction materials are one of the earliest signs of struggles in the supply chain. For instance, general contractors had no choice but to increase their prices due to the escalating prices and availability of materials. As a consequence, these price fluctuations have also negatively impacted their original budgets and caused overruns on certain projects.
The transportation sector is also feeling the heat with increased fuel prices and driver shortages. This has led to longer transit times, resulting in additional storage and handling costs for materials. Marc Powell of StyleAccess LLC, says that for tile importers and manufacturers, the challenge centers on the logistics involved in moving finished goods.
There is a reduction in the availability of containers and a lack of certainty in shipping and arrival dates of goods, which adds to major transportation costs. This results in an eight-fold increase in ocean transport rates.
Furthermore, there is also reduced reliability in local trucking services that are affecting the flow of local raw materials, and even production schedules require constant adjustment based on factors that were not considered pre-pandemic.
2. Delays and Disruptions
One of the main problems affecting job sites is the delay caused by supply chain issues and logistics. Work stoppages and lockdowns at factories continue to have a major impact on the industry and we may see it linger for years. Suffice to say that these current supply constraints are slowing down projects.
Tile and flooring projects require various materials and labor in a job site. It is of utmost importance to time-track everything from buying and shipping materials to doing the job itself. But because of incorrect information on shipment and delayed arrivals, projects are impacted by delays. General contractors, on the other hand, are the ones dealing with unforeseen increases in transportation and material costs.
3. Material and Labor Shortages
The entire construction supply chain is experiencing supply shortages, even with the increased demand for construction materials such as flooring, cabinetry, steel, lumber, and more. The forced pandemic lockdowns created freight issues even to this day, which caused a significant delay in the delivery of a variety, if not all, construction materials. Similarly, supply constraints on building materials such as laminates, tiles, and marble forced contractors to seek alternate materials that are available in the market.
And it's not only materials but people as well that any industry has had a shortage of. With the great resignation still very much happening, this too has taken its toll on the construction industry, which has already been lacking much-needed skilled workers even before the pandemic began.
A report from the US Chamber of Commerce says that 92% of contractors report that they have difficulty finding workers and 42% of those contractors turned down work and projects due to lack of laborers.
4. Backlogs and Paused Projects
Due to the delay in receiving materials, contractors are forced to pause ongoing projects, causing massive delays and backlogs, especially since many customers issued a change in orders as a response to higher costs. This is also very evident with flooring contractors who have waiting lists for their services.
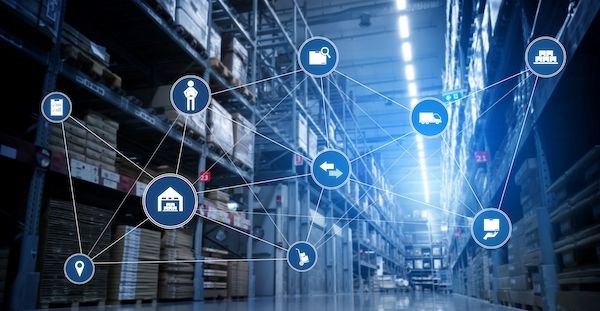
Restructuring Your Supply Chain
In light of the current pandemic-inflicted supply chain issues, flooring contractors need to take a step back and assess their business processes. It is important to revisit and evaluate the following:
- Your sources of supplies
- How you procure materials
- The delivery process of your materials
- Storage of materials and inventory management
- Production processes, labor requirements, and workforce availability
Based on this analysis, it may be necessary for contractors to make some changes as to how they currently operate. There are a few potential solutions that contractors can explore:
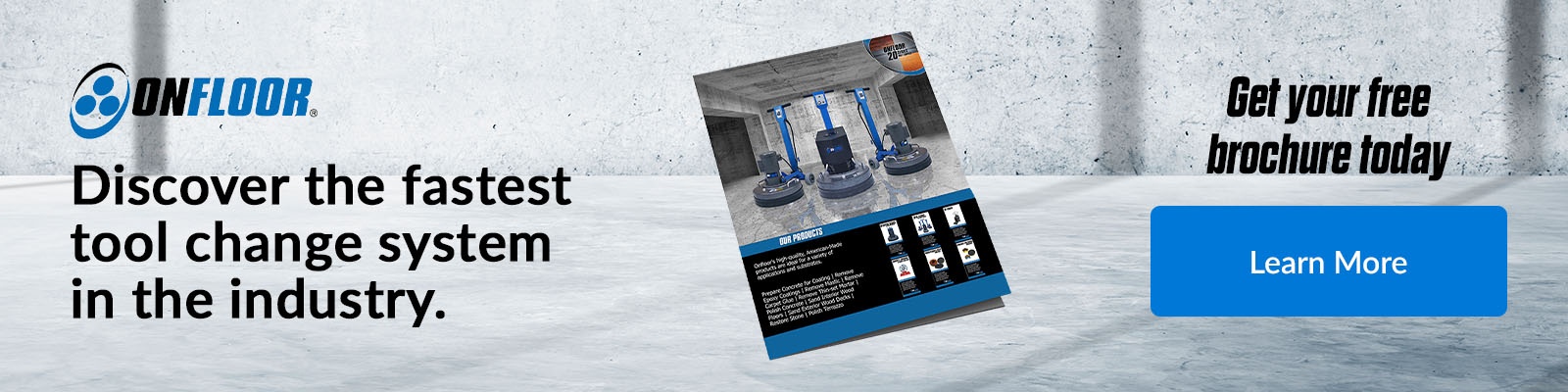
Adaptation and Flexibility
As the whole construction industry continues to move forward, adaptation and flexibility become a critical part of the equation. Flooring contractors, construction companies, and even architectural firms have to be willing to accept alternatives and substitutions in order to execute the existing schedules of the project on time and on budget.
Additionally, there should be an increased commitment to product line rationalization and inventory and not just rely on "just-in-time" thinking. You have to be more flexible in storing and securing materials on a job site and be willing to change up sourcing practices.
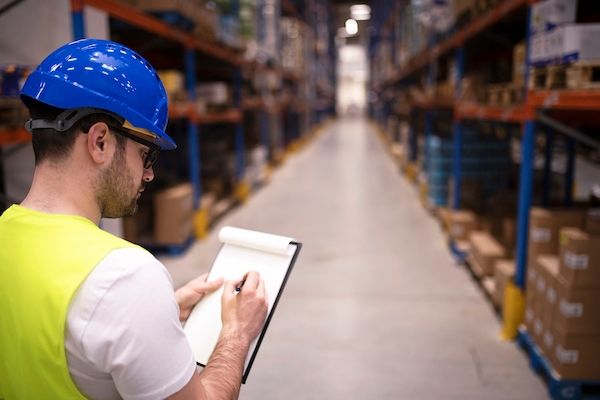
Proper Inventory Management
“Just-in-time” inventory management refers to acquiring goods from suppliers only as needed. This method aims at reducing inventory holding costs and increasing inventory turnover.
The global trend can be attributed to the success of innovations by large corporations such as Toyota, in which inventory reduction is a key factor in magnifying the effects of supply chain problems. And this trend was adopted by distribution firms and manufacturers over the years.
Unfortunately, due to the pandemic, the just-in-time inventory management tactic is not as reliable as it once was. Because there lies the root cause of materials shortages and price fluctuations, the only backup plan available right now is to revert to greater local inventory or face vastly-increased freight costs.
It is important to have a good inventory management system in place so that you can keep track of what materials are available and when they are expected to arrive. This will help to avoid any last-minute rushes to find material or face delays due to lack of supplies.
Collaboration
Collaboration of all kinds is a welcomed idea. According to Pardis Pishdad-Bozorgi, there is a need for "construction-driven design and integration of supply chain participants." Each side has knowledge that can benefit the other in order to move forward with projects in terms of productivity, cost, and schedule and therefore must have strong relationships.
Through collaboration, builders and contractors can explore sustainable ideas to overcome the current supply chain issue. Decisions on alternative delivery methods and materials can be shared, discussed, and addressed early on. Then, implementation to combat these problems can be carried out smoothly, resulting in a timely build.
Intermodal Transportation
When materials are sourced from multiple locations, intermodal transportation can be an effective way to move goods. This involves the transportation of cargo using multiple modes of transport such as truck, rail, and ship which can help to speed up delivery times.
However, this option is only feasible if there is a nearby port or rail yard that can accommodate your needs.
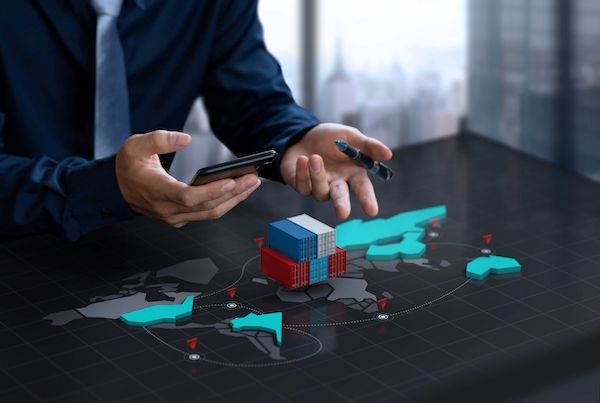
Supplier Diversification
One lesson learned the hard way throughout this whole ordeal is to diversify your supplier base in order to ensure more leverage whenever the need arises. Identify the critical commodity and be sure that you always have options for suppliers for each item. Developing a relationship with more than one supplier will allow for a better balance of risk and give you more leverage when it comes to price negotiations.
However, this also requires increased coordination between suppliers and contractors so that everyone is on the same page with delivery schedules and expectations.
So, if your main supplier should decide to undertake some strategy such as increasing their pricing, or for some reason they find it hard to obtain materials, you can always go to supplier B or C or D. If you have this leverage, you have the advantage of avoiding delays and disruptions.
Effective Planning and Communication
The success of any project depends largely on the planning and communication between team members. This is especially important when it comes to working with suppliers.
To combat the current supply chain issues, flooring contractors should take the time to plan each project carefully and communicate with suppliers early on. This will help to avoid any misunderstandings or delays down the road.
For efficient production planning, contractors need to carefully plan their production schedule and prioritize the most critical items. In some cases, it might be necessary to delay non-critical tasks to ensure that essential items are completed on time.
It is also important to plan for potential disruptions and have backup plans in place. This will help to minimize any negative impact on the project timeline.
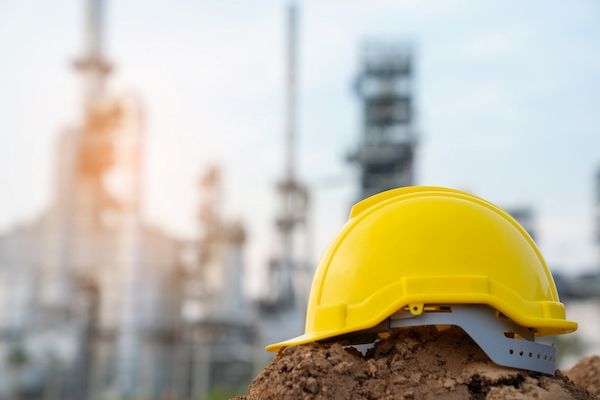
Resilience Amidst Supply Chain Issues
Flooring contractors need to be resilient and adaptable in order to combat the current supply chain issues. By planning carefully, communicating effectively, and diversifying the supplier base, you can minimize the impact of these problems on your projects.
Nonetheless, the construction industry will continue to thrive despite adversity and uncertainty because of its resilient build and ability to find solutions. These challenges will only serve as a learning experience for contractors, suppliers, and builders alike as they navigate through price increases and material delays.
Being proactive in proven methods, rethinking old strategies, and being innovative, flexible, and collaborative are the only ways to move forward.
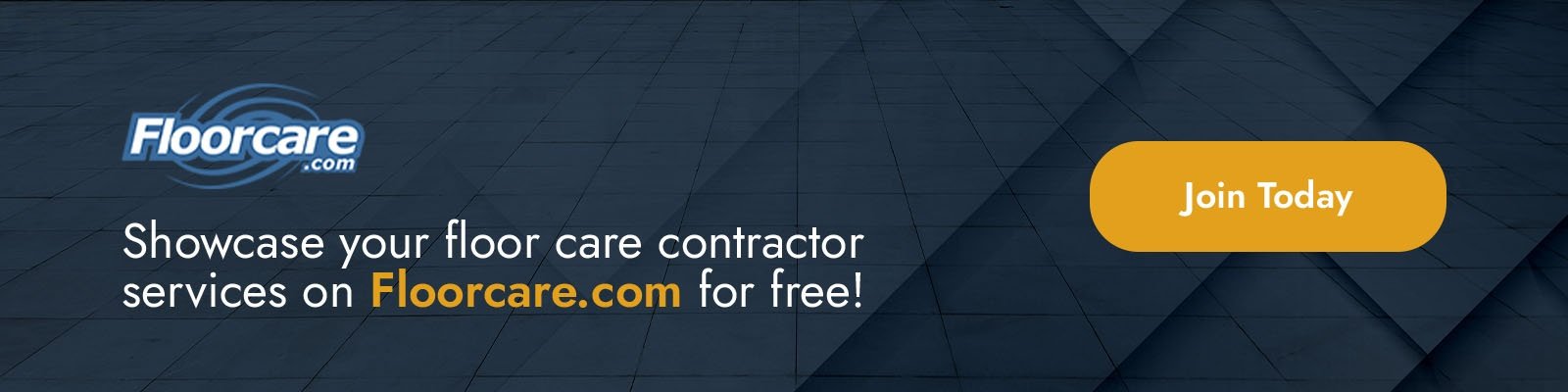
1 Comment