There are hardly any structures in our environment where you won’t find concrete, the second most widely used material. From the foundations to the core of skyscrapers and other essential areas, concrete remains an irreplaceable building material. Nonetheless, it is always necessary to manipulate it after curing it to fit the purpose.
Shaping the concrete requires machines, one of which we will discuss today. The long life it enjoys can be enhanced with finishing processes, including epoxy coating or the use of marble. Whichever is the case, the concrete grinding wheel is often the equipment of choice for preparing the surface.
We’ll explain how this specialized wheel works, including the types and how to pick the right one. The grinder you need for smooth finishing will differ from the one for uneven surfaces. Here is all you need to know about these abrasive tools and how they can help you manipulate cured concrete.
The Concrete Grinding Wheel
The grinding wheel consists of abrasive particles with a bonding agent holding them together in an edged pattern. These are not conventional abrasives but materials sharp enough to cut independently, making it so you can cut materials or sand down a surface for a smooth finish.
You can use these abrasive particles to remove concrete sealers on the surface, paint, or rust. In addition, they come in various sizes and shapes to fit the power tools, which include angle grinders.
These grinding wheels have coarse-particle aggregate such as:
- Ceramic
- Silicon carbide
- Aluminum oxide
- Cubic boron nitride
While these are tough abrasive particles, the diamond wheel is the hardest. It is more common and preferable for cured concrete of any hardness.
Components
There are two primary components to a concrete grinding wheel. That includes the abrasive stones and the bonding agent. Then, you have the floor or angle grinders that hold them during operation on the site.
Any brand you get uses the same components. The abrasive coating removes material from the surface through high-speed rotation. Hence, the floor's or angle grinder's power matters when deciding how much material you want to remove from the surface.
The finish determines which abrasive material to fix to the floor or angle grinder. So, you have power, size, and abrasiveness as contributing factors to delivering a good job.
You will change the stone more often, as it will wear with prolonged contact with the surface. Nonetheless, the wheel's life depends on how much you use it.
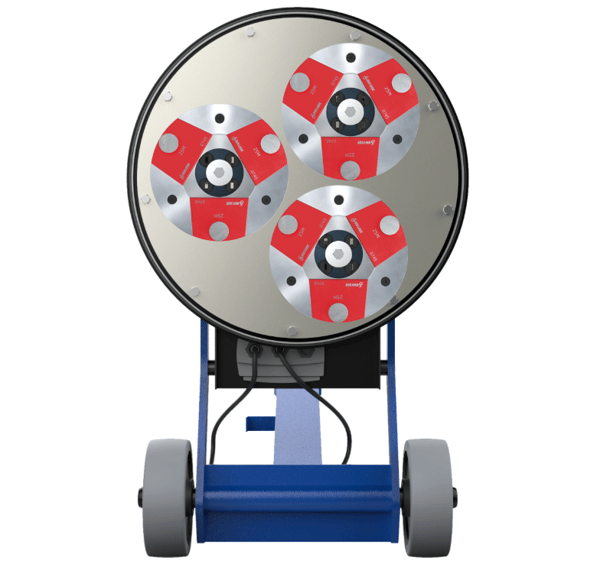
Characteristics
How would you determine which wheel is best to grind your sidewalk or garage for epoxy? We have identified a few aspects to pay attention to before you purchase one for your project. These are criteria that a professional considers before making a purchase.
The specifications include the following:
- The material hardness
- The grain size and the coarseness
- The wheel grade, which comes from the bonding agent
- The spacing between the grains
- The bond type
So, consider these specifications before you get your new supply of grinding wheels. The suppliers will often ask for them when you order.i
Why You Need a Concrete Grinding Wheel
Preparing the concrete is essential for many things, from smoothing to preparing it for staining or coating. The tool is handy in the hands of a professional, whether on a floor or angle grinder.
Here are the benefits of getting grinding wheels for your project:
- They improve the surface finish, which increases durability.
- They increase efficiency through high performance and quick work.
- You will save costs as they are harder while maintaining lower prices.
Your productivity as a professional will increase when you get the right wheels for the job. Whether replacing or repairing a new concrete floor, you will need these wheels. That smooth grinding is possible.
How to Use a Concrete Grinding Wheel
The first step to using the grinding wheel is getting a floor or angle grinder. Changing the wheels is easy, whether on a handheld angle grinder or the push-around floor type.
Then, you can turn on the power tool and guide the wheel over the concrete. The process always involves dry grinding. Do not use floor or angle grinders, like the Milwaukee, on a wet floor.
You’ll have a smooth floor at the end of the process. The natural stone's coarseness will give way to a better finish.
Places you can use this machine include garages, factories, warehouses, and concrete building walls.
Types of a Concrete Grinding Wheel
One thing a professional does best is pick the appropriate tool for the job. These wheels come in different types for different purposes. For example, a wheel with a high diamond concentration has a separate application from one with silicon carbide.
With that in mind, here are the types of wheels you need:
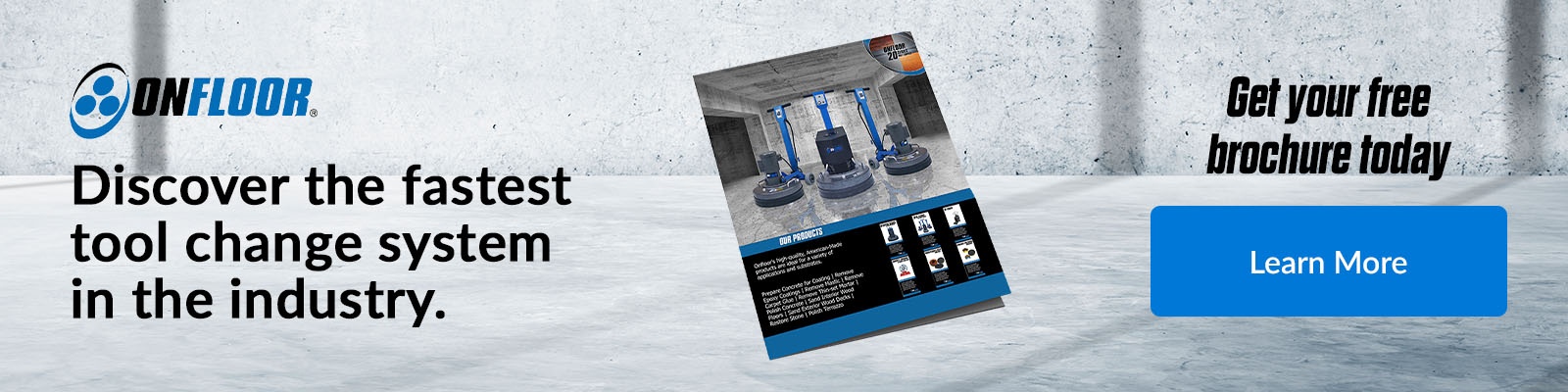
Straight Grinding Wheels
This wheel is the most essential tool you can purchase from manufacturers or suppliers. They work well on polishing small concrete areas and are the best deals for home use. You’ll find them versatile enough for several applications.
Straight grinding wheels are not ideal for more extensive work areas, both in shape and durability.
Grinding Cup Wheels
Cup wheels are the most common you’ll find for polishing stones. Pick a diamond grit to remove adhesive and other tough materials from surfaces.
Depending on the job delivery, these wheels can reach 36 inches in diameter. However, prices increase as the size increases. The smaller ones work perfectly with handheld angle grinders, like the Milwaukee.
Because of their large sizes, you can use a cup wheel in walk-behind floor grinders. The diamond cup wheels are the best in this segment.
Grinding Dish Wheels
The major difference between the dish and cup wheels is the surface age. Cup wheels have a thicker surface edge, unlike dish wheels. Also, the dish wheel is more shallow.
If you were to spend money on a tool for thinner areas and tight holes, the dish wheel is the ideal fit. It can fit much better than the diamond cup grinding wheel in tight holes.
How about getting a diamond cup grinding wheel and dish wheels to account for their unique applications? Most angle grinders can handle both, allowing you to use them interchangeably. Moreover, they deliver different grinding styles that help you get even, smooth flooring.
Diamond Segmented
Wheels with a higher concentration of diamonds cost more. However, they have excellent delivery on smooth floors. You can pick any level, from fine to coarse.
Silicon-Carbide
The silicon-carbide type has you covered if you want a cost-effective approach. It produces a fine and coarse finish but clogs too often, making it unsuitable for large areas.
Tungsten-Carbide
The tungsten-carbide type is ideal if the price is no problem and you need perfect delivery. Its carbide-tipped blocks and beveled edges work well to remove higher thicknesses, like 1 inch.
The tungsten-carbide type leaves no scratches on the stone after grinding. It also has high durability during high power operations.
Picking the Right Grinding Wheel for the Job
Diamond fittings are the best all-around tools for concrete grinders. Their price may not be low, but they can work on any material, regardless of its hardness. Also, they will not break halfway as they contact the floor.
With a ten on the Mohs hardness scale, longevity and durability are not a challenge them. The prices may be a deciding factor, but there are other things to account for. There are other considerations when picking the perfect wheel for your job.
- The size should fit the power tool you intend to use. Ensure the diameters match inch for inch.
- Consider the number of ribs. Multirib wheels, like the double or triple ribs, have more intensity in contact with the floor and produce better surfaces. However, the price is high and may not fit in handheld grinders.
Selecting the Grit Type
The grit type determines how much material you remove in a run. Confirm whether you must remove less than an inch or more.
Fine grits are ideal for smoothing and polishing. Coarse grits remove thicker surfaces or coatings. Often, your job will require both coarse and fine grits.
Proper Storage and Safety Precautions
Here are things you must keep in mind regarding safety and storage:
Safety Precautions
Grinding services must be done with the appropriate personal protective equipment. Your eyes and ears should be adequately covered because of the splatters that will fly.
Ensure your workplace is free of trip hazards. Cables should be neatly dressed and securely plugged in. Finally, be mindful of cracks that might lead to breakage.
Storage
Whether you use diamond tools or the silicon-carbide types, keep them in dry storage. Do not stack them when not in use.
Tips on Optimizing the Concrete Grinder
Let’s wrap up with a few tips to optimize your concrete grinding services with the right wheel:
- Do not push the revolutions per minute.
- Apply even pressure for a smoother surface.
- Apply downward pressure for faster grinding
Conclusion
The concrete grinding wheel is used to smooth and polish cured concrete. It works through a power tool that provides power and rotary motion for material removal.
If unused, a wheel can last for two years after manufacture. You can also use them for other materials, including granite, stone, and brick. However, pick a diamond cup wheel if you work on delicate surfaces.
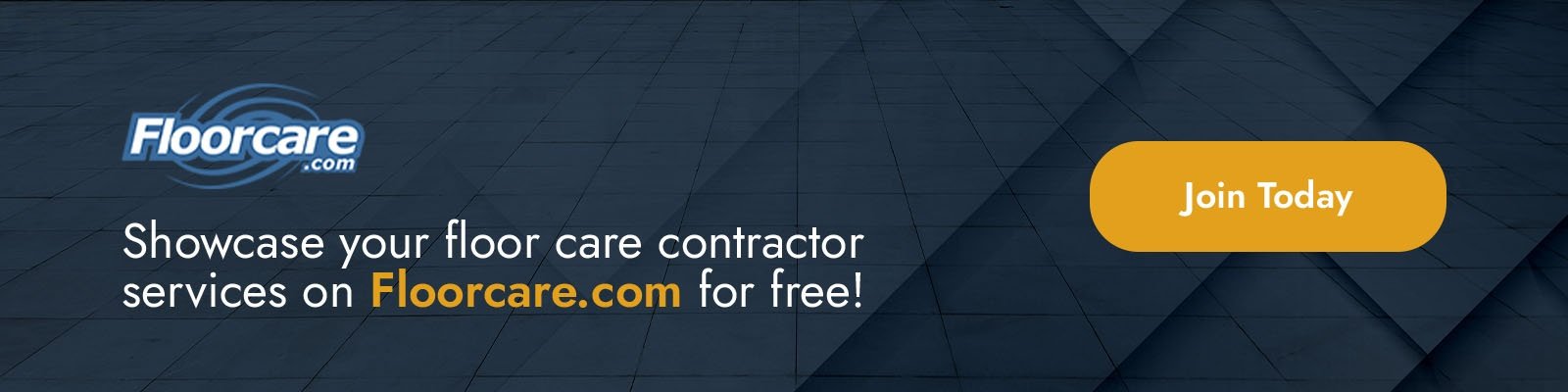
0 comments